Purification of Contaminated Soils
The ECOREFINE technology is a process for purifying soils contaminated with pollutants or other materials (e.g. mill scale sludge) in ‘on-site operation’. This purpose-built system can be operated both mobile and stationary.
The new procedure is founded on vacuum evaporation and enables time-saving and rapid decontamination without the use of any additives. The contaminated material is continuously fed into a vacuum container via inlet sluices and heated as it passes through.
The moist components (water and various carbohydrate compounds) evaporate in the process. These vapours are extracted from the container, separated from dragged dust particles and then condensed. The purified material leaves the container through outlet sluices.
Most of the solid and liquid end products obtained in this way can be recycled. Soil can be reused for agricultural purposes after being mixed with water and bacteria. The metal powder obtained from the grinding sludge can be fed into blast furnace treatment; most of the separated carbohydrates (oils) can be further processed. Already in 1994, this process has already been realized in a pilot plant and tested for its functionality in numerous trials. Continuous investigations by TÜV Thüringen and other institutions have shown that maximum cleaning results are achieved with this process.
ECOREFINE FOR SLUDGE
Capacity: 50 tons/hour
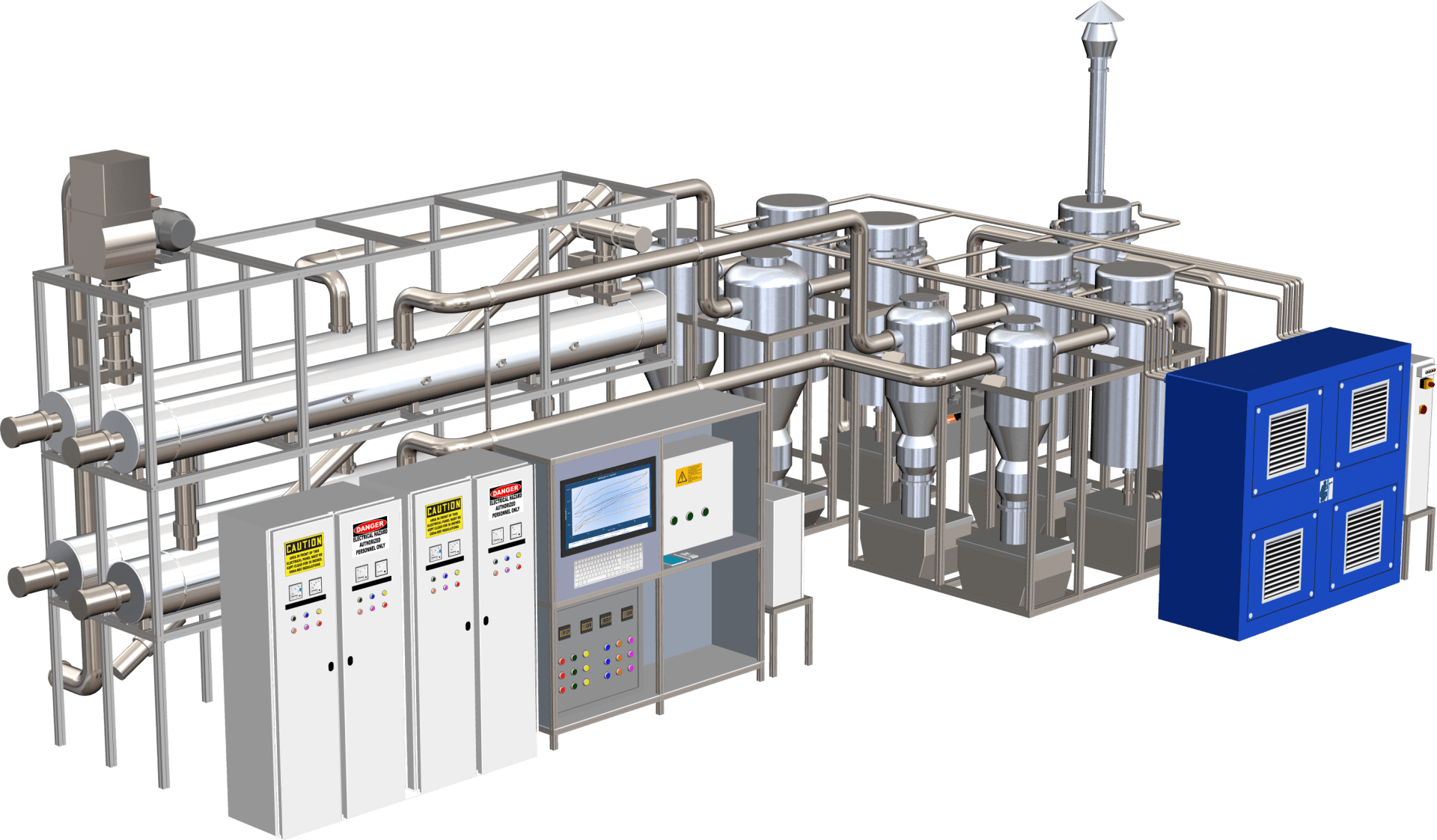
ECOREFINE – Description
Once the contaminated oil sludge has been inserted into the plant, a vacuum is created in the double sluiced chamber-off system. Through a further sluice, the material falls onto compressed air controlled plate vibrators. The vacuum and heat during this process cause the hydrocarbons to gasify, whereby dirt particles in the oil are filtered out through a dust separator. After cooling the substances down, oil and sand are being separated. The machinery and procedures for this process have been industrial approved.
The system entails the following, especially for this process developed components:
- Process valve
- Exhaust
- Vacuum pump
- Cyclone separators
- Condenser
- Cooling System
- Double chamber system
The system consists of several closed, externally insulated vessels that are equipped with appropriate interior conveyors, such as paddle mixers and screw conveyors. The individual containers are directly connected to each other by means of suitable support mechanisms and an intervening double sluice chamber system.
The interconnected vessels of the system have an inlet and an outlet double sluice chamber system. The vessels are equipped with heating and heatable exhaust systems. In addition, the system has vacuum generators, suitable separators, condensation systems and, if necessary, a power supply system.
From the hopper, the contaminated material enters into an inlet double-lock chamber system. As soon as the level indicator has registered the exact inflow, the central system closes the upper sluice. A vacuum is generated in the sluice system which, in conjunction with the vacuum in the tank, maintains the correct flow rate. The lower sluice opens and oil sludge falls into the tank to be transported by paddle mixers or screw conveyors.
Likewise, devices for droplet separation from gases and for the separation of liquids can be obtained. A heated dust separator is located between the vessels and the respective condensation units. An emission condenser with a suitable filtration device is installed behind the vacuum generation units. In addition, the plant has rotary vacuum feedthroughs that can withstand temperatures of up to 350°C.
The plant is equipped with a programmable logic controller (PLC) that is connected to sensors in the overall system. The liquid in the oil sludge is gradually evaporated. An operating pressure (pressure level) and an operating temperature (temperature level) can be adjusted in each tank (4 tanks in total), which are located between the double sluice chamber system.
The purified oil leaves the vessel system through the double sluice chamber system. The steam and gaseous substances are discharged, cleaned (dedusted) in the separators and liquefied in the condensers. The exhaust steam condenser with its filter behind the vacuum generation unit ensures almost emission-free operation. The separated particles from the gas and the separated liquid are discharged from the vacuum by appropriate devices and collected in a vessel. Depending on the quality and processing, they can be returned to the process stream.
The entire system will consist of 4 large tanks, each with 2 double sluice chambers. In the current process, the viscosity of the oil sludge changes from vessel to vessel. The two end products are sand with a dryness level of 99.9% and the 100% purified crude oil.
A separate area within the plant is designated for processing the purified materials, using technologies and equipment such as a gas chromatograph.
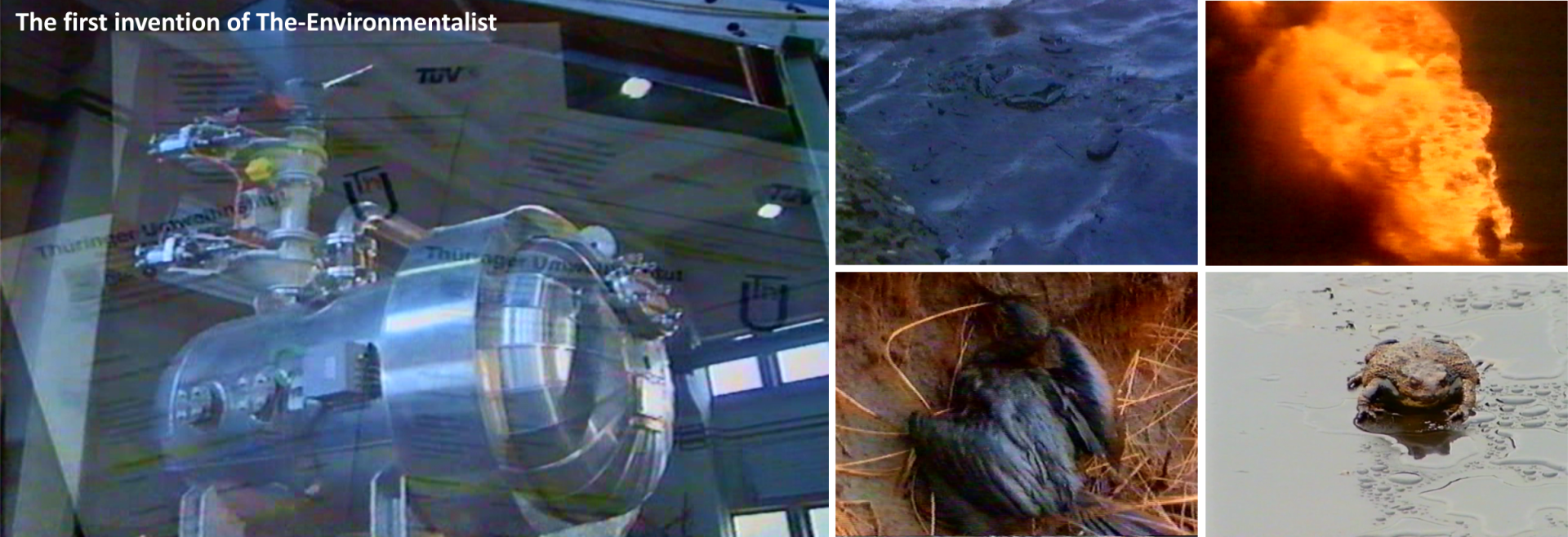
The ECOREFINE system works extremely efficiently and can clean up to 100,000 kg of contaminated material per hour, while the closed system guarantees clean and silent operation. The process produces very low pollutant emissions, with levels well below regulatory limits (a fraction of the amount of pollutants emitted by an average modern car).
The ECOREFINE is suitable for the treatment of contaminated industrial material such as grinding sludge, mill scale sludge, sludge from oil production and processing, and contaminated construction waste. PREUSSAG's cleaning of mill scale sludge showed excellent results. Mill scale sludge is an oil-contaminated waste product from steel processing. After separation of oil and water, the dry substance can be immediately reused as a raw material for sintering processes, resulting in considerable economic advantages.
TÜV Thuringia has certified and confirmed the functionality of ECOREFINE: "The results confirmed the applicability of the process in principle for the decontamination of the soil samples at hand. A purification rate of up to 99.3% was determined. Further advantages of ECOREFINE are its mobility and thus its diverse application possibilities, as could be demonstrated. The on-site cleaning avoids long transport routes of contaminated material. The ECOREFINE will occupy an important position in the existing market, both technologically and economically.
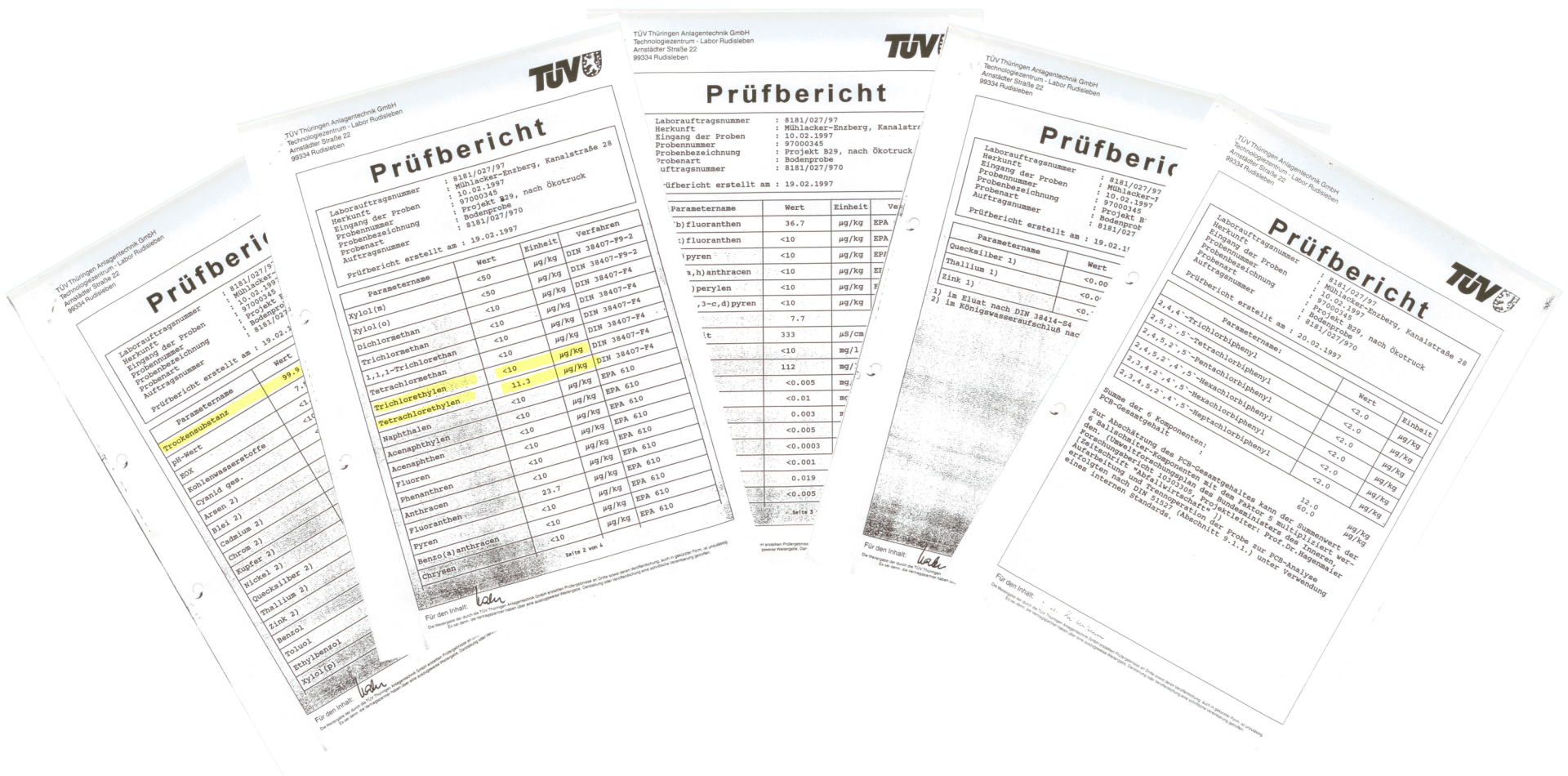
Before Ecorefine: Tetrachloroethylene 52,200.00 µg / kg
After Ecorefine: Tetrachloroethylene 11.30 µg / kg
Purification in %: 99.98
Operational Possibilities on the Market
The ECOREFINE is able to vaporise substances* from contaminated material. These often found substances are listed in the following:
- Mineral hydrocarbons (MHC), e. g. crude oil, heating oil, diesel, petrol etc.
- Benzene, toluene, ethyl benzene, xylene (BTEX)
- Polycyclic aromatic hydrocarbons (PAHC)
- Halogenated hydrocarbons (HHC)
- Phenols
- Cyanide
- Heavy metals in volatile compounds
* The substance to be separated from the material has to reach a vapour pressure of at least 1 millibar at a maximum temperature of 300°C.
The quality of the purified products according to the legal regulations is warranted by continuous laboratory tests. The outstanding results and advantages of this decontamination procedure are absolutely innovative in comparison with conventional methods. Finally, the convincing aspects of the ECOREFINE can be summarized as follows:
- high purification results (certified test results)
- high throughput
- mobile and stationary plant
- high flexibility
- efficient and economic operation
- no additives required for the process
- clean and ecologically beneficial process
- cost reductions (no expenses for transport and storage)
- reusable final products
- reduction of disposal expenses